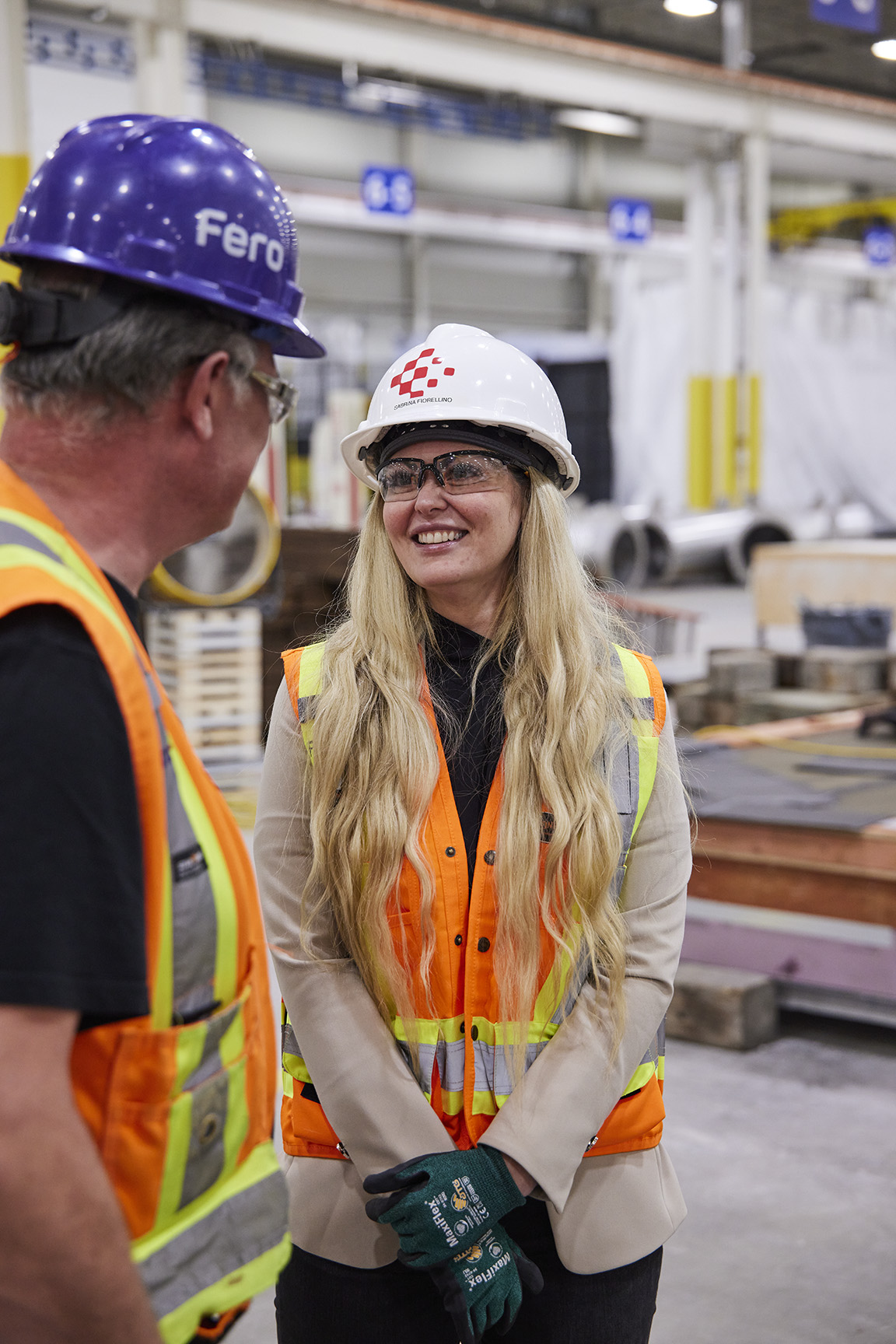
Building Green
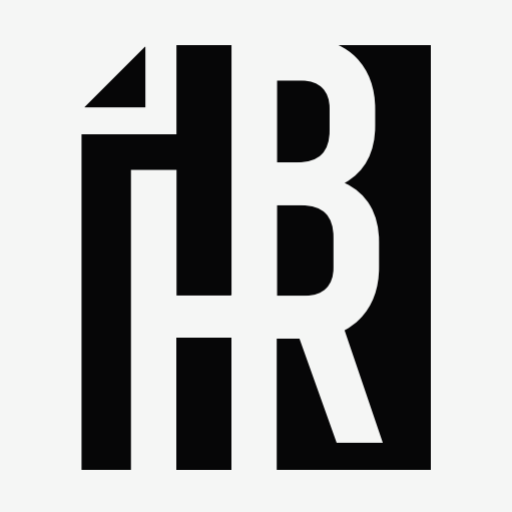
Written by: Ian VanDuzer
Fero’s modular construction strategy keeps carbon emissions down
In this age of climate change awareness, we are all familiar with particular benchmarks: “green energy” means power generated using renewable resources, like solar and wind; your “carbon footprint” is how much carbon dioxide you’re responsible for emitting; a “passive house” is incredibly energy efficient – and therefore better for the environment (and also, apparently better at surviving raging wildfires).
One term is new, but is quickly picking up steam: Embodied Carbon.
If you’re not familiar with the term yet, get ready to hear it – a lot – especially as governments and builders work overtime to address the housing crisis gripping Hamilton and beyond. It’s the measure of emitted carbon throughout a product’s entire lifetime, including elements that are often overlooked, like emissions relating to transporting raw materials to the plant, and the processed material from the plant to the build site. Embodied carbon is a more complete, holistic view of the greenhouse emissions relating to our buildings, which is quickly making it the prime benchmark for regulation agencies and governments.
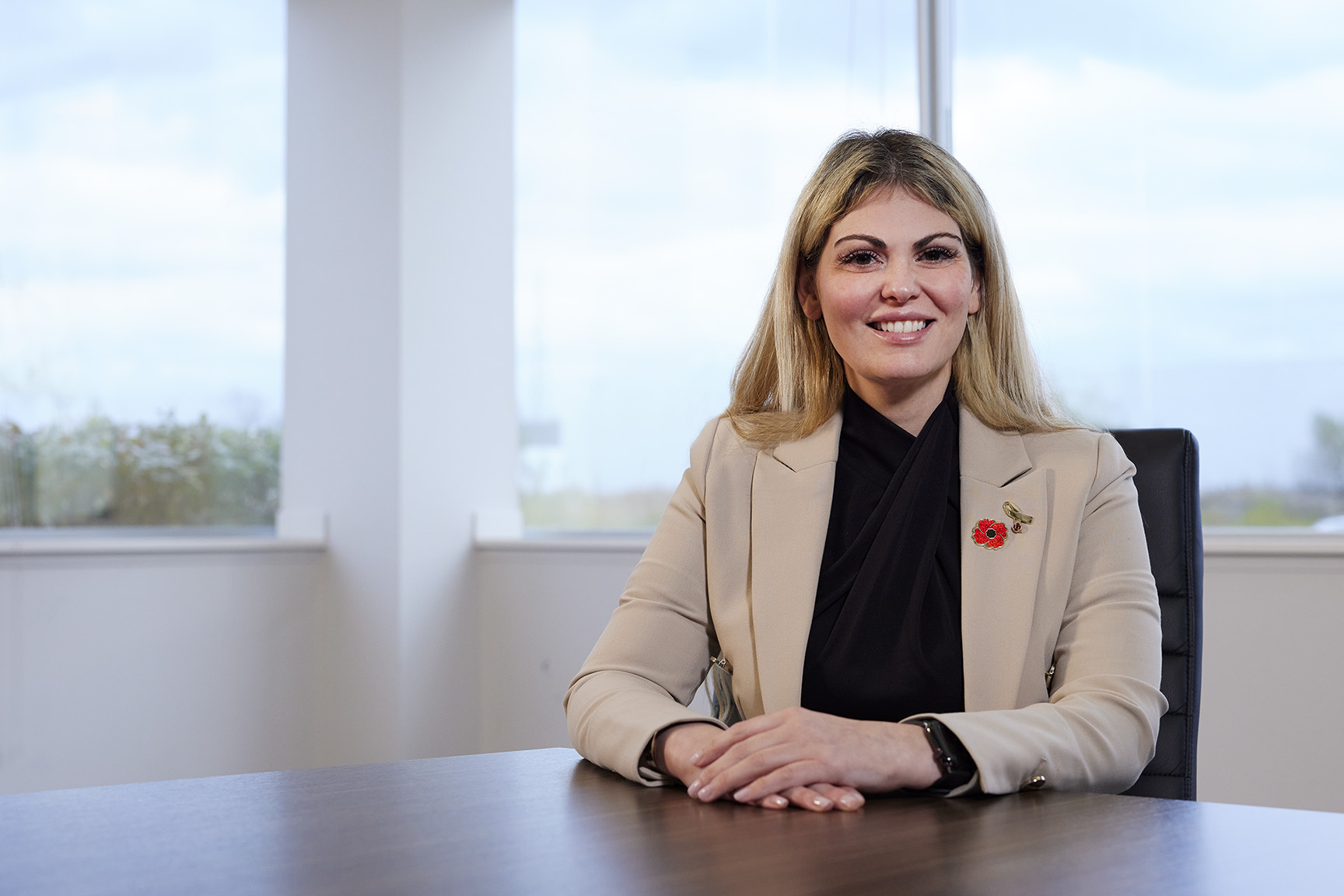
With its increased focus, builders and entrepreneurs are racing to meet incoming standards and future-proof their processes. Some are seeking to refine their material selection, or are focusing on projects closer to home.
And then there are others, like Stoney Creek-based Fero International, who are taking a different approach to sustainability.
“We believe that our system is more sustainable in general than traditional construction,” explains Sabrina Fiorellino, the founder and CEO of Fero International. Fero designs, constructs, ships, and assembles modular buildings across Canada, doing most of the construction at their 300,000 square foot manufacturing facility in Stoney Creek.
Modular construction may be newer to us in North America – where modular construction currently has a meagre 3% market share – but it’s a system that is growing in popularity in Europe and Asia, where it’s booming up to 80% of construction in some countries. “It fits a lot of current needs,” Fiorellino says.
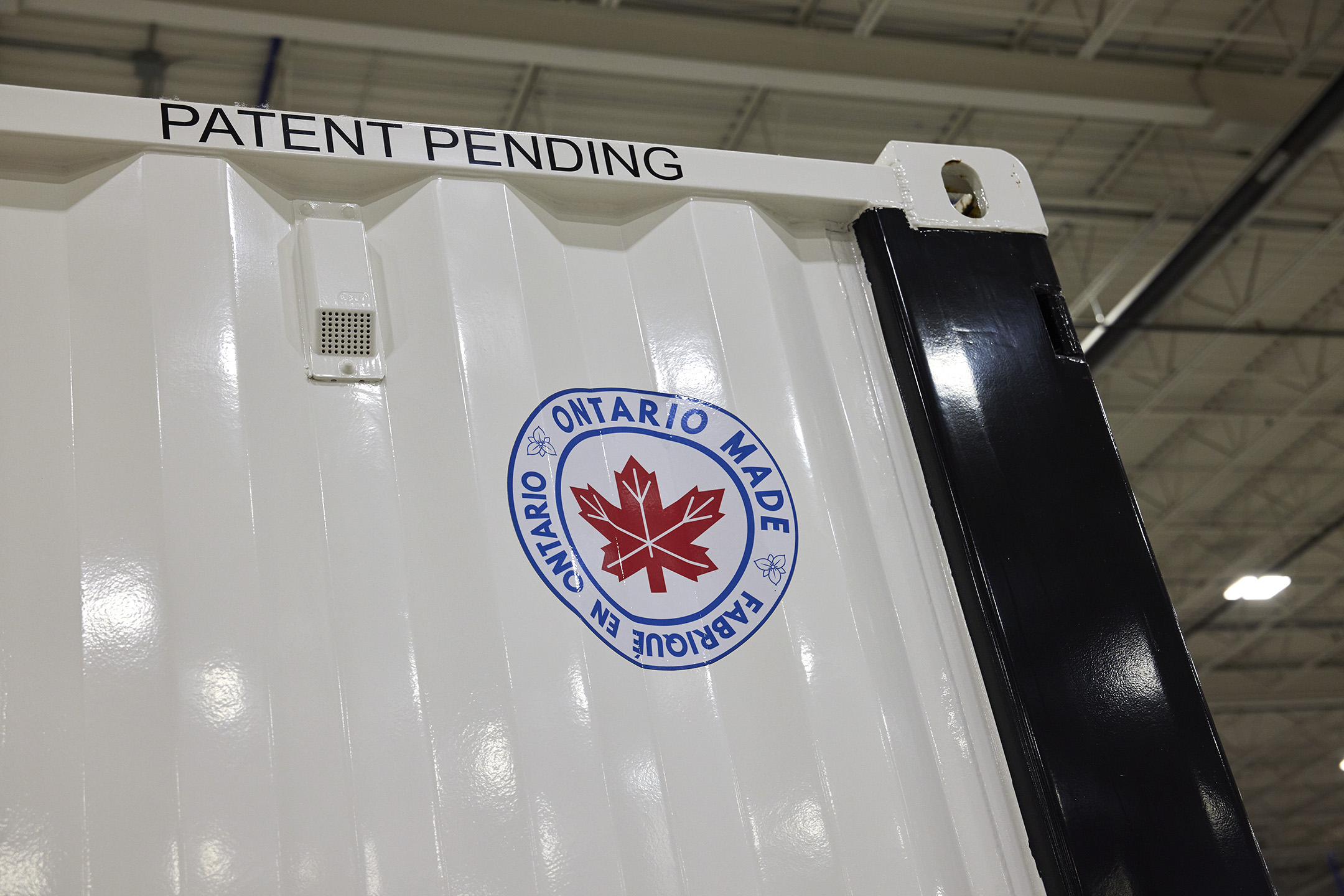
Founded in 2020, Fero’s initial focus was quickly creating healthcare spaces for hospitals that suddenly needed increased capacity (they’ve built expansions to hospitals in Manitoba and Ontario, with future projects in other provinces). They’ve since expanded their focus to fit the most-pressing needs of our society: education and housing. All three sectors are heavily involved with government spending and programs, and so are also the most concerned about embodied carbon.
Fiorellino believes that Fero’s methods are inherently advantageous when it comes to meeting carbon emissions targets. “We don’t have lines of trucks going to the construction site every day,” she points out. That means that Fero has more flexibility in terms of what materials they can use in their projects, since their process results in lower embodied carbon. It also gives Fero incredible ability to take on projects anywhere in Canada while still keeping construction and jobs in Hamilton (“We see us always being in Hamilton,” Fiorellino says reassuringly).
Automation has also helped streamline the construction process for Fero, helping to lower material costs for their clients and projects. “We have some automation that cuts our sheet goods – our plywood and drywall – makes our frames, and reintroduces our offcuts of steel back into the process,” says Fiorellino.
The result is remarkably little waste throughout the entire construction process, as multiple projects can be in progress at once, and materials can easily be shared between them. The lack of waste isn’t only confined to the process: take a stroll through Fero’s manufacturing facility and you’ll be hard-pressed to spot garbage cans of any kind.
Automation also speeds up overall construction time and reduces the number of on-site specialists needed, keeping costs down for their projects.
The final piece of the puzzle for Fero’s sustainability efforts is deconstructability. “Buildings have a lifespan,” Fiorellino says. “And when that lifespan ends, most buildings are demolished, and the majority of those materials don’t get recycled or reused – because they weren’t designed that way.”
In contrast, Fero buildings are designed to be deconstructed – which is less satisfying to watch than a controlled demolition with loads of TNT, but much better for the environment. “It’s a lot easier to reuse the materials in our projects,” notes Fiorellino. That cuts the embodied carbon content on future developments, too, since reusing materials means you don’t have to emit carbon to mine and refine raw materials from scratch.
“With traditional construction, you might be able to get to Net Zero emissions,” notes Fiorellino.

“But you can’t get better than that. If you reuse materials, suddenly you have the potential to do even better from a decarbonizing perspective.”
– Sabrina Fiorellino, Fero International Inc.
See what's possible. Bring your discovery to market.
Related Articles
Related
Powering the Future
AP Renewables’ new tool helps out the little guyAmin Ahmadi wants you to imagine that you own a fleet of cars. It’s the metaphor that he feels best describes the challenges facing wind farm operators today. And if that seems like a bit of a stretch, hear him out.“Cars...
McMaster and Local Hospitals Personalize Cancer Treatment
"'The Juravinski Research Institute (JRI) is supporting a groundbreaking project by Hamilton Health Sciences, McMaster University and St. Joseph’s Healthcare Hamilton that could transform cancer treatment in Hamilton and serve as a model for cancer care across...
McMaster PhD Student Uses AI to Predict Fractures
"Could AI be used to assess fracture risk for older adults? That’s the question at the heart of research being done by PhD student Edward Chu, who is exploring how machine learning could predict fractures in older adults with osteoporosis. Currently, when health-care...